
치과용 구강 스캐너와 모델 스캐너를 이용하여 제작된 보철물의 변연적합도
Abstract
The purpose of this study was to compare the marginal fit of the dental prosthesis with the oral scanner and the model scanner. The model(3-unit bridges) used urethane material on the chamfer margin. The urethane model was scanned with a oral scanner and a model scanner, and then designed with CAD software. Each test piece was made of a subtractive manufacturing and an additive manufacturing process. The marginal fit was measured using a replica technique. We analyzed the marginal opening(MO), the marginal gap(MG) of the maximum curvature area, the axial gap(AG), and the occlusal gap(OG) with a CCD camera mounted on a microscope. And then, the distance was measured using an image analysis software. In order to analyze the changes of the scanning method and the manufacturing method, two-way ANOVA was performed. For data of each parameter, a one-way ANOVA was conducted.
Overall, the average value of the marginal fit was less than 169μm, and the average value of MO and AG was 79 μm or less. There was no difference in the mean values of MO and AG in the prosthesis milled by subtractive manufacturing with oral scanner and model scanner. MG, OG showed better fit of the prosthesis made by the oral scanner than the prosthesis manufactured by the model scanner.
Keywords:
marginal fit, oral scanner, model scannerⅠ. 서 론
최근 디지털 기술을 이용한 치과용 보철물의 제작은 빠르게 발전하고 있다. 특히 CAD/CAM(Computer Aided Design/Computer Aided Manufacturing) 기술을 이용한 지르코니아 보철물 제작은 현재 가장 많이 적용되고 있는 분야이다(Miyazaki 등, 2009; Tuthard 등, 2009; Kim 등, 2016).
치과 보철물을 제작하기 위한 통상적인 방법은 구강내 형태를 인상하여 채득한 인상체에 석고 모형재를 주입하여 구강내 형태를 모형으로 재현하고 이를 직접 사용하여 보철물을 제작하는 것이다. 반면에 디지털 기술을 이용한 치과 보철물 제작 방법은 석고모형을 스캐닝(scanning)하여 구강내 형태를 컴퓨터에 데이터 베이스(data base)화 하고 (Miyazaki 등, 2009; Ender 등, 2003) 이로부터 보철물을 디자인하며 디자인된 보철물의 데이터를 절삭가공(subtractive manufacturing)과 적층가공(additive manufacturing) 장비로 가공⋅출력하여 보철물을 제작하는 것이다.(Rekow, 1993). 절삭가공은 블록(Block)형태의 재료를 삭제하여 원하는 형태의 보철물을 제작하는 방법으로 대표적인 장비로 치과용 밀링머신(Milling Machine)이 있다. 적층가공은 액상 또는 분말 형태의 재료를 여러개의 층으로 쌓아 올려 원하는 형태의 결과물을 얻어내는 방법으로 대표적인 장비는 치과용 3D-printer가 있다(Figure 1).
디지털 기술을 이용한 보철물 제작은 3차원 스캐너(3D scanner)의 출현으로 시작된 것이라 할 수 있다. 3차원 스캐너는 접촉식과 비접촉식 방식이 있으며, 접촉식은 모형의 표면을 센서가 접촉하여 3차원의 데이터로 얻어내고 비접촉식은 레이져빔을 모형에 조사(scanning)하여 3차원의 데이터를 얻어내는 방식이다(May 등, 1993; Beuer 등, 2008). 초기에는 접촉식 스캐너가 주로 사용되었으나 스캐닝에 소요되는 시간이 매우 길고 센서가 접촉하지 못하는 부위는 정밀도가 낮았다. 이런 이유로 최근에는 비접촉식 스캐너가 더 많이 사용되고 있다.
치과기공소에서 주로 사용하고 있는 비접촉 스캐너는 인상체나 인상체에서 얻어진 석고 모형을 스캐닝하는 모델 스캐너(model scanner, MS)가 대표적이다. 최근에는 진료실에서 환자의 구강내를 직접 스캐닝하는 구강용 스캐너(oral scanner, OS)가 개발되었다(Rekow, 1993). OS는 인상체와 석고 모형이 필요 없으므로 재료 소모와 제작시간을 줄일 수 있으며 구강내 색조도 파악이 가능하다는 장점이 있다. 그러나 지금까지 OS와 MS에 대한 정보는 많이 부족한 편이며, 특히 각각의 방식으로 제작한 보철물의 정밀도에 대하여 비교 분석한 연구는 발표되어 있지 않다.
이에 본 연구에서는 동일 모형에 대하여 OS와 MS로 스캐닝하고, 스캔된 데이터를 사용하여 절삭가공(밀링머신)과 적층가공(3D printer)으로 제작한 보철물에 대하여 적합도를 비교 분석하여 치과 보철물 제작의 임상적 검토를 확보하고자 한다.
Ⅱ. 재료 및 방법
1. 브리지 모형 제작
3-unit 모형을 제작하기 위해 스테인레스 금속 모형을 제작하였다. 금속 모형은 소구치용 지대치는 지름 7 mm, 높이 10 mm로 대구치용 지대치는 지름 11 mm, 높이 10 mm의 형태로 제작하였다. 또한 3-unit의 가공치 부분의 공간을 부여하기 위해 소구치와 대구치 중앙부로부터 20 mm 설정하였다. 제작된 금속 모형은 밀링머신(F4, Degudent, Germany)에 6° 밀링바 (Tungsten carbide bur, Hopf Ringleb & Co., Germany)를 장착하여 chamfer 형태의 변연으로 밀링 가공하였다. 또한 교합면은 중앙부 깊이가 1 mm가 되도록 하여 원뿔 형태로 하였고 교합면 우각 부분은 부드럽게 이행되도록 연마하였다(Figure 2). 이렇게 제작된 금속 지대치 모형은 실리콘 인상재로 복제하였고 우레탄 모형재(Polyurock, Metaux, Germany)로 주 모형 6개를 제작하였다(Kim 등, 2014).
2. 모델 스캔
6개의 주 모형은 각각 구강용 스캐너(Trios, 3shape, Denmark)와 데스크용 스캐너(D700, 3Shape, Denmark)를 이용하여 스캐닝하였다. 스캔된 각각의 STL 파일은 디자인 프로그램(3shape model builder, 3Shape, Denmark)이용하여 변연 1 mm 상방으로 두께 30 µm의 시멘트 공간을 부여하고 12개의 계속가공의치 보철을 디자인하였다(Figure 2).
3. 보철물 제작
디자인이 완성된 데이터는 절삭가공 장비 밀링머신(DEG-5X100, Arum, korea)에 PMMA블럭을 장착하여 OS와 MS로 디자인된 12개의 보철물을 절삭 가공하였다. 이때 밀링버는 새 bur를 장착하여 가공하였다. 또한 적층가공 장비 3D-printer(PRO JET 3500, 3D systems, USA)를 이용하여 동일한 12개의 데이터를 레진 패턴으로 적층 가공하였다. 완성된 레진 패턴은 2종류의 스캐너(OS, MS)와 두 가지의 제작방식에 따라 각 6개씩 총 24시편이 준비되었다.
4. 적합도 측정
밀링머신과 3D-printer로 제작된 보철물의 적합도를 측정하기 위하여 실리콘 복제법을 사용하였다. 주 모형과 보철물 사이에 light body 실리콘(Smart sil, Seilglobal, Korea)을 채운 후 손가락으로 1차 시적 후 50N의 정하중기 압력에서 실리콘이 경화되도록 유지하였다. Light body 실리콘이 완전히 경화되면 우레탄 주 모형에서 보철물을 제거하고 아크릴 시트지로 박싱하여 regular body 실리콘(Charmflex, denkist, Korea)을 채운 후 포매하였다. 완전히 regular body 실리콘이 경화된 후 협설 중앙부위를 근원심 방향으로 표기 후 컷터칼날을 이용하여 절단 분리하였다(Figure 3). 절단된 실리콘 시편은 실체현미경(S39A, MIC, USA)과 디지털 현미경 카메라(Eyecam, MIC, USA)를 이용하여 x100배율로 촬영 캡쳐하였다. 캡쳐된 사진은 이미지분석 소프트웨어(Toupview 3.5, MIC, USA)를 사용하여 내면 적합도를 측정 분석하였다. 이때 측정부위는 보철물의 끝 모서리 부분과 지대치 변연의 부분에 틈을 marginal opening(MO), 지대치 변연으로부터 상방 400 µm에서 거리를 marginal gap(MG)로 측정하였다. 또한 지대치 축면을 axial gap(AG), 교합면의 중앙부를 occlusal gap(OG)로 하여 측정하였다. 측정은 소구치 지대치 근원심에서 각각 측정한 평균값과 대구치 지대치 근원심에서 각각 측정한 평균값을 사용하였다. 본 연구에서 지정한 측정부위를 실체현미경으로 촬영한 사진이다(Figure 4).
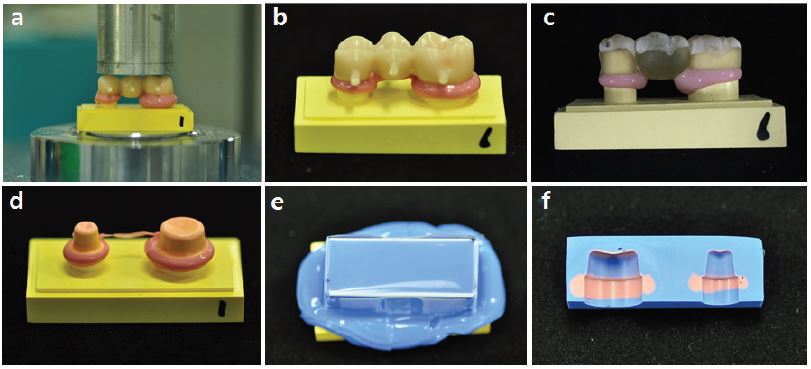
Measurement process. (a) 50N Pressure of Standard weight device, (b) PMMA crown made with CAD-CAM, (c) resin crown made with 3D-printer, (d) crown is removed from the model (e) investment of heavy body silicone (f) crown is removed from the model final cut specimens.
5. 통계분석
각 영역에서 사용된 스캐너와 제작방법이 미치는 영향을 알기 위하여 이원배치분산분석(two-way ANOVA)을 실시하였다. 또한 각 그룹 간 평균값들의 통계적 차이를 알아보기 위해 일원배치분산분석(one-way ANOVA)과 scheffe’s test를 시행하였다. 통계분석은 SPSS version 21 (SPSS Inc., USA)을 이용하여 유의수준은 p<0.05 수준으로 결정하였다.
Ⅲ. 결 과
제작한 보철물의 스캔 방식과 제작방법에 따른 각 영역에서 적합도 평균값은 Table 1에 정리하였으며, Figure 5는 이를 그래프로 나타낸 것이다. 전체적인 적합도의 평균값은 <169 µm로 나타났으며 MO, AG의 평균값은 <79 µm의 값을 보였다. 측정부위 MO, MG, OG에서는 구강용 스캐너와 모델 스캐너로 가공 밀링한 보철물(milling)의 적합도가 적층가공한 보철물(3D-pinter)보다 좋은 적합도를 보였으며 측정부위 AG는 스캐너와 제작방법에 상관없이 <50 µm의 값을 보였다.
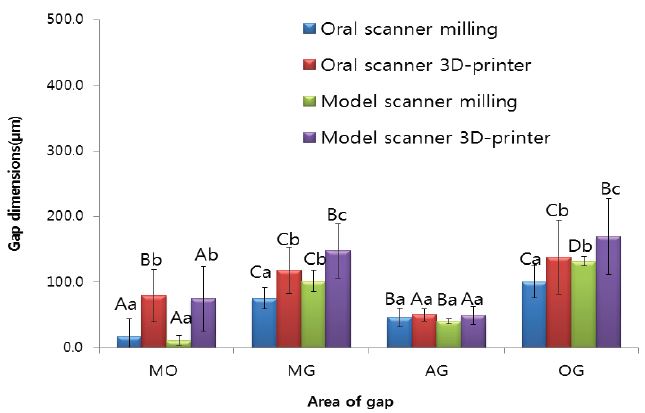
Mean gap dimensions of resin patterns.Mean values groups with the same characters mean statistically insignificance at p<0.05 level.The upper-case letters are for comparison between scanner and manufacture method.The lower-case letters are for comparison between gap area.
구강용 스캐너와 모델 스캐너로 절삭 가공한 보철물에서 MO, AG의 평균값은 차이가 없지만 MG, OG에서는 모델 스캐너로 밀링 제작한 보철물의 평균값이 구강용 스캐너로 절삭가공한 보철물보다 크게 나타났다. 이는 적층가공한 보철물에서도 동일하게 나타났다. 또한 측정부위 OG에서는 다른 측정부위에 비해 가장 큰 값을 나타냈다.
Table 2는 각 내면적합 측정부위에서 스캐너와 제작방법에 따른 이원배치분산분석 결과이다. MO와 AG는 제작방법에 따른 유의한 차이가 나타났으며 MG, OG에서는 스캐너 유형 또는 제작방법에 따라 유의한 차이가 나타났다(p<0.05).
Ⅳ. 고 찰
임상적으로 치과 보철물의 적합도는 가장 기본적으로 요구되는 사항이다. 특히 변연 적합도가 좋지 않으면 지대치와 보철물 사이에 음식물 잔사와 플라그 형성으로 인한 치은염, 치주염 그리고 2차 우식증을 야기시킬 수 있다(Felton 등, 1991). 이에 치과 보철물의 적합도에 대한 평가는 임상적으로 중요하다. 적합도 평가를 위해서는 환자 구강내에 보철물을 장착 후 보철물의 상태를 직접 관찰하는 것이 가장 좋다. 그러나 실질적으로 좁은 환자 구강 내에서 적합도 평가를 하는 것은 대단히 어렵다. 이에 대부분에 연구에서 동일한 시편을 제작하여 시편 위에 보철물을 만들어 평가를 한다(Carter 등, 1983). 본 연구에서도 금속을 이용하여 지대치 모형을 제작 후 실리콘으로 복제된 우레탄모형 시편을 사용하였다. 이때 3-unit 브리지의 형상은 자연치아의 크기를 참고하였고, 변연의 형태도 균일하게 chamfer 변연으로 밀링하여 제작하였다.
실험용 시편을 사용하여 제작되는 치과 보철물도 중요하다. 대부분의 선행연구에서 CAD/CAM 장비를 사용하여 지르코니아, 연질 합금과 같은 재료를 가공하여 적합도를 측정하였다. 그러나 이러한 재료들은 소결과정을 거치면서 재료들의 오차가 발생할 수 있다. 이에 본 연구에서는 오차 범위를 줄이기 위해 new bur를 장착 후 가공하기 쉽고 소결 과정이 필요 없는 PMMA 블록을 사용하였다. 또한 같은 데이터를 가지고 3D-printer로 제작 되어진 레진 패턴의 값을 함께 비교 분석하고자 하였다.
시편과 보철물의 내면 적합도를 측정하는 방법은 직접 절단해 보는 방법과 간접적으로 절단해 보는 방법이 있다(Sorensen 등, 1990; Moon 등, 1998; Kim 등, 2016). 직접 절단해 보는 방법은 시편과 보철물을 시적 후 포매 하여 내면부위를 절단하여 보는 방법으로 내면의 모습을 그대로 볼 수 있는 장점이 있다 그러나, 시편의 수가 많이 필요하고 동일한 모형에서 다른 보철물을 제작해서 측정하기는 어렵다. 간접적으로 절단해 보는 방법은 내부 공간에 실리콘을 채워 실리콘의 두께를 측정하는 방법이다(Molin 등, 1993; Rahme 등, 2008; Bayramoglu 등, 2015). 이 방법은 주 모형의 파손 없이 여러 개의 보철물을 제작해서 반복 측정할 수 있다. 본 실험에서는 스캔 방식과 제작 방법에 따른 적합도 측정 시 모형 손상 없이 측정할 수 있는 간접법을 이용하여 측정 분석하였다.
간접 측정방법을 사용하여 어느 부위를 비교 분석하였는지도 중요하다. 선행연구에서 Holmes 등(1989)은 수복물 변연과 지대치 변연 사이의 거리를 absolute marginal discrepancy라고 하였고 수직⋅수평에 대한 변연 거리를 각각 horizontal marginal⋅vertical marginal gap 이라 하였다. 또한 지대치의 안쪽 내면에서 수복물 내면까지의 수직 거리를 internal gap이라 하고 지대치 변연부에서 수복물 수직거리(overextended)와 수복물 변연에서 지대치 수직거리(underextended)를 marginal gap이라고 하였다. 또한 Beuer 등(2009)은 서로 다른 지르코니아를 제작하여 지대치에서 변연 끝 사이 거리를 marginal opening(MO)로 하고 chamfer 변연의 가장 깊은 곳에서 보철물 내면까지의 거리를 CA라 하였다. 본 연구에서 적합도 측정부위 MO는 Holmes 등(1989)의 AMD와 일치하며, 지대치 변연 가장 오목한 부위에서 보철물의 수직거리인 MG(marginal gap)를 측정하였다. 이때 MG(오목한 부위)의 측정부위는 측정마다 달라질 수 있기에 때문에 지대치 변연에서 400 µm 상방에서 측정하였다. OG 및 AG은 각각 이름은 다르지만 Beuer 등(2009)이 측정한 위치와 같다.
적합도 간격의 임상적 수용 가능성에 대한 평가 기준도 다양하게 보고되고 있다. Assif 등(1987)은 평균적인 변연간격이 약 140 µm라고 보고하였고 Mclean 등(1971)은 5년 이상된 보철물을 조사하여 120 µm 이하의 변연간격은 수용 가능하다고 보고하였다. 따라서 본 연구에서도 선행연구에서 제시한 최대 허용 기준인 120 µm를 적합도 기준으로 설정하였다. 본 연구에서 측정된 적합도는 절삭 가공한 보철물의 경우 120 µm이하의 값을 전체적으로 나타나 기준치에 부합하였으나, 3D-printer로 제작된 보철물 MG, OG는 120 µm이상의 값을 보여 기준치를 상회하는 것으로 나타났다. 특히 모델 스캐너를 이용하여 적층가공한 OG는 169 µm의 값을 나타내어 측정값 중 가장 큰 나타났으며, 절삭 가공한 MO는 11 µm로 가장 작은 값을 나타내었다.
본 연구의 측정위치에 대한 평균 비교 결과 MO, MG, OG에서는 OS와 MS로 절삭 가공한 보철물(milling)의 적합도가 적층 가공한 보철물(3D-pinter)보다 좋은 적합도를 보였다. 또한 이원배치분산분석 결과에서도 측정부위 MO, MG, AG, OG는 제작방법에 따른 유의한 차이가 나타났다. 이는 보철물 제작 시 밀링머신으로 제작한 보철물이 적합도가 좋은 것을 의미하며 선행 연구에서 김등(2014)도 3D-printer로 제작한 보철물의 적합도는 다소 크게 나타났다. 이에 향후 3D-printer의 정밀도는 개선이 필요할 것으로 사료된다.
OS와 MS로 절삭 가공한 보철물에서 MO, AG의 평균값은 큰 차이가 없이 비슷한 적합도를 보였다. 하지만 MG, OG에서는 OS로 절삭 가공한 보철물의 적합도가 좋게 나타났다. 이는 인상채득 후 석고 모형 제작과정에서 오는 오차 범위와 MS의 스캔 오차라 보여진다. 따라서 OS는 MS만큼의 성능과 그 이상의 정밀도를 가졌다고 사료된다. 본 연구의 제한점으로는 두 개의 스캐너만 비교하였으므로, 향후 추가적으로 다양한 OS를 이용한 비교연구가 필요하다고 생각된다. 또한 진료실에서 치과위생사가 OS를 이용한 스캔작업이 이루어지기 때문에 CAD/CAM 시스템의 원리와 과정을 잘 이해하고 OS의 조작방법을 정확히 숙지한다면 손쉽게 인상채득을 할 수 있을 뿐 아니라 보철물을 제작 시 정확한 보철물을 제작 가능하여 환자에게 만족할 만한 결과를 줄 수 있으리라 기대된다.
Ⅴ. 결 론
본 연구에서는 구강용 스캐너와 모델 스캐너를 사용하여 스캔된 데이터를 디자인한 후 절삭가공(밀링 머신)과 적층가공(3D-printer)으로 제작한 보철물에 대하여 적합도를 비교 분석하여 다음과 같은 결론을 얻을 수 있었다.
- 1. 본 연구에서 제작된 모든 적합도의 평균값은 <169 µm로 나타났으며, MO, AG의 평균값은 <79 µm의 값을 보였다.
- 2. 측정부위 MO, MG, OG에서는 구강 스캐너와 모델 스캐너를 사용한 절삭 가공한 보철물(milling)이 적층 가공한 보철물(3D-pinter)보다 양호한 적합도를 보였다.
- 3. 구강 스캐너와 모델 스캐너로 밀링 가공한 보철물에서 MO, AG의 평균값은 차이가 없지만 MG, OG에서는 모델 스캐너로 절삭 가공한 보철물보다 구강용 스캐너로 절삭 가공한 보철물의 적합도가 좋았다.
- 4. 측정 부위 MO와 AG는 제작방법에 따른 유의한 차이가 나타났으며 MG, OG에서는 스캐너 유형 또는 제작방법에 따라 유의한 차이가 나타났다(p<0.05).
따라서 구강용 스캐너는 모델 스캐너보다 정밀한 보철물 제작이 가능한 수단이 될 수 있으며, 밀링머신에 비해 3D-printer를 이용한 보철물은 향후 개선이 필요할 것으로 사료된다.
Acknowledgments
* 시편제작에 도움을 주신 유정치과기공소 송두빈 소장님께 감사드립니다.
References
- Assif, D., Rimer, Y., Aviv, I., (1987), The f low of zinc phosphate cement under a full-coverage restoration and its effect on marginal adaptation according to the location of cement application, Quitessence Int, 18(11), p765-774.
- Bayramoglu, E., Kulak, Y., Yildiz, C., (2015), Comparison of marginal and internal fit of press-on-metal and conventional ceramic systems for three- and four-unit implant-supported partial fixed dental prostheses: An in vitro study, J Prosthet Dent, 114, p52-58.
-
Beuer, F., Naumann, M., Gernet, W., Sorensen, J., (2009), Precision of fit: zirconia three-unit fixed dental prostheses, Clin Oral Investig, 13, p343-349.
[https://doi.org/10.1007/s00784-008-0224-6]
-
Beuer, F., Schweiger, J., Edelhoff, D., (2008), Digital dentistry : an overview of recent developments for CAD/CAM generated restorations, Br Dent J, 204(9), p505-511.
[https://doi.org/10.1038/sj.bdj.2008.350]
-
Carter, JM., Sorensen, SE., Johnson, RR., Teitelbaum, RL., Levine, MS., (1983), Punch shear testing of extracted vital and endodontically treated teeth, J Biomech, 16, p841-848.
[https://doi.org/10.1016/0021-9290(83)90008-8]
-
Ender, A., Mehl, A., (2003), Accuracy of complete-arch dental impressions a new method of measuring trueness and precision, J Prosthet Dent, 109(2), p121-128.
[https://doi.org/10.1016/s0022-3913(13)60028-1]
-
Felton, D., Kanoy, B., Bayne, Sa, Wirthman, G., (1991), Effect of in vivo crown margin discrepancies on periodontal health, J Prosthet Dent, 65(3), p357-364.
[https://doi.org/10.1016/0022-3913(91)90225-l]
-
Holmes, JK., Bayne, SC., Holland, GA., sulik, WD., (1989), Considerations in measurement of marginal fit, J Prosthet Dent, 62, p405-408.
[https://doi.org/10.1016/0022-3913(89)90170-4]
- Kim, SC., Han, MS., Choi, BJ., Lee, CJ., Lee, HH., (2014), Internal fit of bridge patterns fabricated by a 3D printing technique, Kor J Dent Mater, 4, p239-244.
- Kim, SC., Lee, HH., (2016), Marginal Accuracy of Three-Unit Bridge Fabricated Using Dental Co-Cr CAD/CAM Soft Metal Block, Kor J Dent Mater, 2, p177-184.
- Luthard, RG., Weber, A., Rudolph, H., Quaas, S., Walter, M., (2009), Design and production of dental prosthetic restoration: basic research on dental CAD/CAM technology, Int J Comput Dent, 5(3), p165-176.
- May, KB., Russell, MM., Razzoog, ME., Lang, BR., (1993), Precision of fit:the Procera AllCeram crown, J Prosthet Dent, 80(2), p394-404.
- McLean, JW., Von Fraunhofer, JA., (1971), The estimation of cement film thickness by an invivo technique, J Br Dent, 131, p107-111.
-
Miyazaki, T., Hotta, Y., Kunii, J., Kuriyama, S., Tamaki, Y., (2009), A review of dental CAD/CAM: current status and future perspectives from 20 years of experience, Dent Mater J, 28(2), p44-56.
[https://doi.org/10.4012/dmj.28.44]
-
Molin, M., Karlsson, S., (1993), The fit of gold inlays and three ceramic inlay systems: A clinical and in vitro study, Acta Odontol scand, 51(4), p201-206.
[https://doi.org/10.3109/00016359309040568]
- Moon, BH., Yang, JH., Lee, SH., Chung, HY., (1998), A s tudy on the marginal fit of all-ceramic crown using ccd camera, J Kor Acad Prosthodont, 36, p273-292.
- Rahme, HY., Tehini, GE., Adib, SM., Ardo, AS., Rifai, KT., (2008), In vitro evaluation of the "replica technique" in the measurement of the fit of Procera crowns, J Contemp Dent Pract, 9, p25-32.
- Rekow, ED., (1993), High-technology innovations and limitations for restorative dentistry, Dent Clin North Am, 37(2), p513-524.
-
Sorensen, JA., (1990), A standardized method for determination of crown margin fidelity, J Prosthet Dent, 64, p18-24.
[https://doi.org/10.1016/0022-3913(90)90147-5]